Cement, Lime & Alumina
Cement plants, lime plants and alumina refineries are all under pressure to reduce costs by minimising refractory maintenance repairs and extending the run-time between shutdowns. In cement plants refractory linings, anchors and metallic structures face harsh operating conditions undergoing pervasive chemical attack and can prevent plants achieving their desired refractory life. Rotary kilns typically dictate campaign length, and too often refractory failures force shutdowns to be brought forward. Lime plants face similar issues but usually to a lesser degree, however older plants can experience reliability issues and unnecessarily high maintenance costs.
Our Services
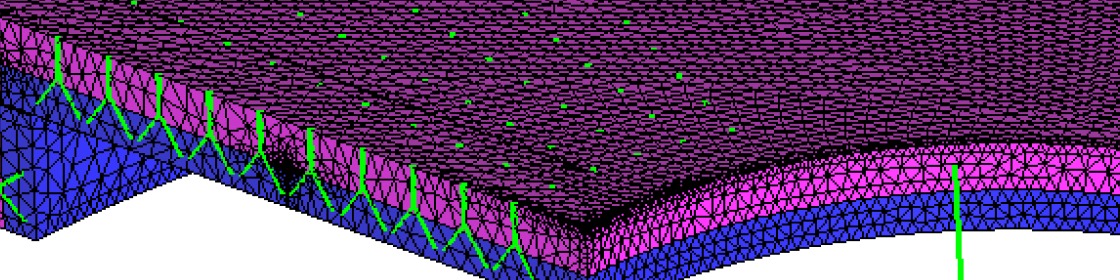
Monolithic Refractory Design
We have a proven successful record in refractory and mechanical designs for cyclones, ducts, roofs, coolers and calciners. By taking a combined engineering approach, our designs match materials to your process, engineer anchoring for increased life, stop shell corrosion and increase energy efficiency. This results in improved reliability and helps you extend time between maintenance.

Non-Destructive Testing
Our P-Response technology can survey refractory anchored to any flat steel surface. It improves safety by generating a refractory damage map that allows contractors to remove damaged overhead panels. Furthermore, it reduces maintenance costs and shutdown time by ensuring only precision repairs are carried out.
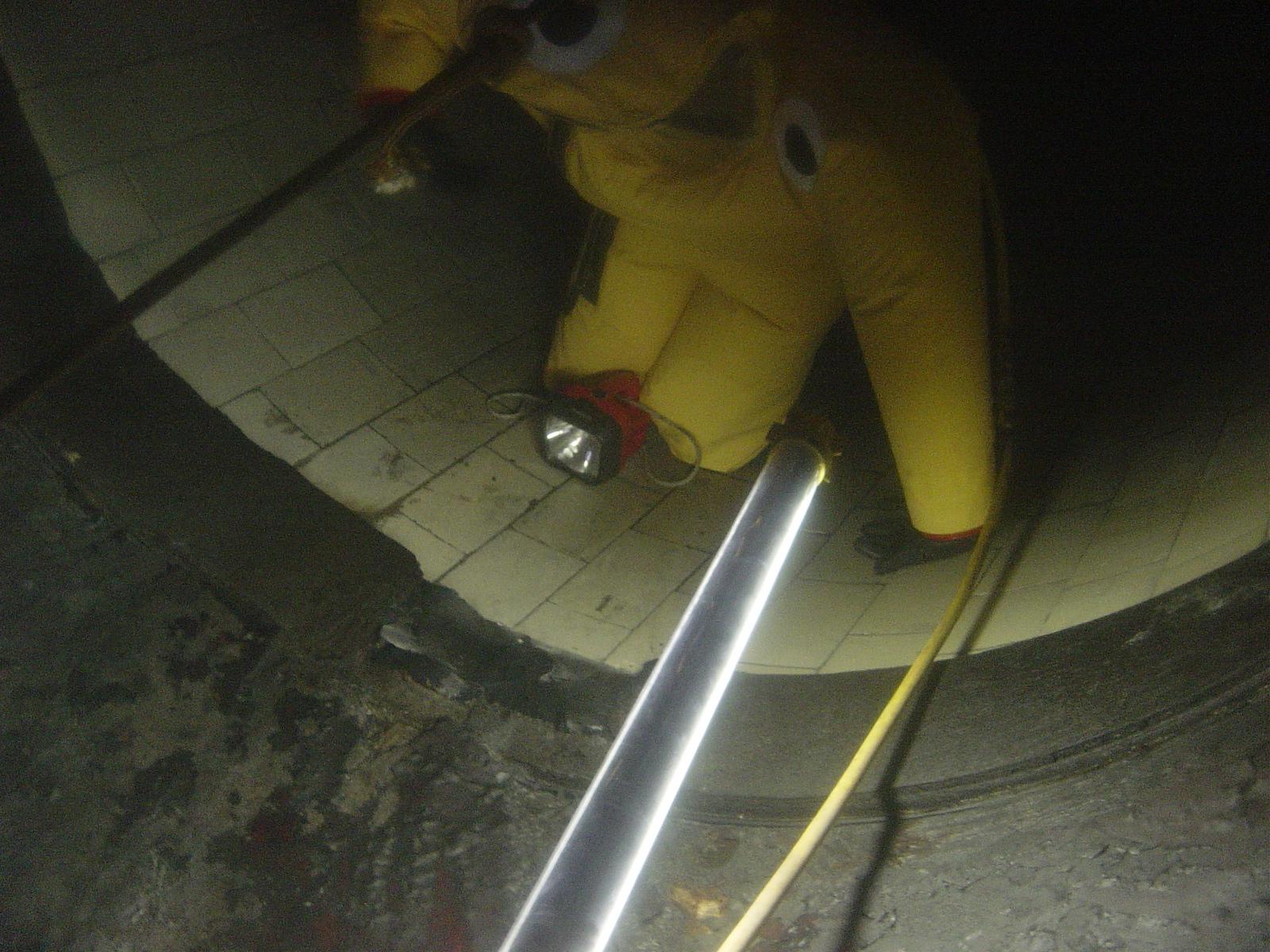
Shutdown Support
Our professional material and process engineers can independently assess the refractory repair scope required to meet reliability goals and ensure unnecessary repairs are avoided. We can generate ‘on the spot’ technical solutions that account for site material limitations and provide technical solutions to emergent problems within the resource constraints of the shutdown. Additionally, we provide future work scopes for the next shutdown.
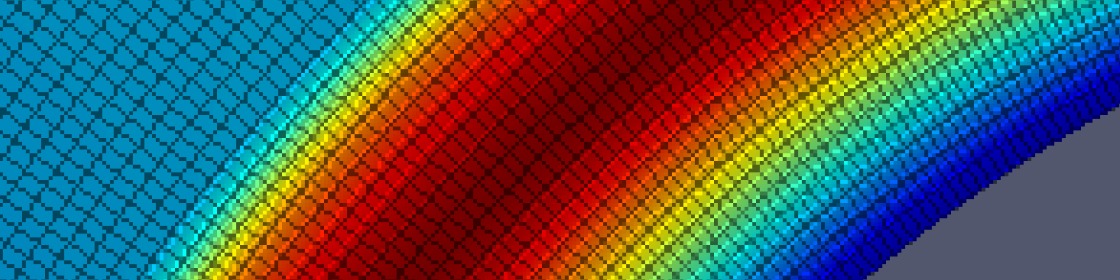
Refractory Dryouts
Typical industry dryout schedules assume ambient conditions, which does not effectively mitigate risk for pressurised processes. Additionally, these dryouts attempt to cater for all plant configurations and variations resulting in substantial inefficiencies. Our bespoke dryouts use proprietary software to calculate the most optimal, safe dryout by targeting your plant geometry, material properties, process environment and burner capacity. We have helped customers safely reduce their dryout time by over 50%.
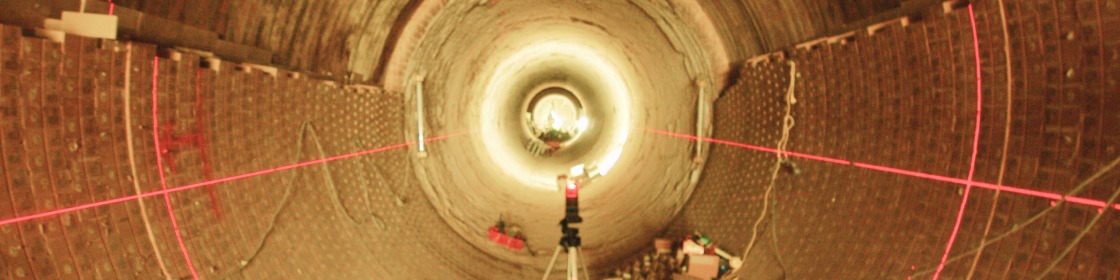
Rotary Kiln Refractory
It is well known that kiln ovality and shell distortion impact refractory life. Bricking handbooks set the correct goals for bricking over shell distortions but offer no methods or objective limits to achieve improved reliability. We can analyse the kiln ovality and shell distortion data that you already collect to create a bricking plan tailored specifically to each local distortion. In addition, our analysis can set achievable and measurable quality assurance guidelines specific to your kiln and brick supply.
Additionally, brick material optimisation is typically done by trial and error which can be a slow and costly pathway to improvements. Through scientific analysis, we can recommend materials that directly address the degradation mechanisms specific to each section of the kiln and process.
It is through this scientific approach that plants can achieve their desired reliability goals.
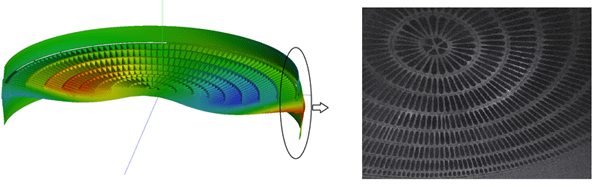
Failure Analysis
When acid linings show signs of degradation, i.e., cracks, it is very important that any assessment/investigation correctly identifies the underlying mechanism and its condition. Our expertise in material assessment/analysis to extends to development of effective testing regimes, and interpretation that translates to real-world improvements. In combination with our computer simulation & modelling capabilities, we have helped clients correctly identify the root causes, failure criteria and provided simple solutions.
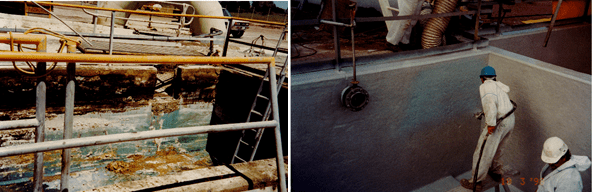
Concrete Assessment & Repairs
We specialise in the assessment of concrete structures degraded by corrosion, chemical attack, thermal stress, weathering. We undertake assessment of your structures, identify key failure mechanisms, and carry out repairs. Our experts are familiar with silos, stacks, sulphur pits, effluent tanks, plinths, columns, and other structures.
Our Clients

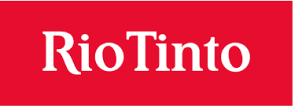
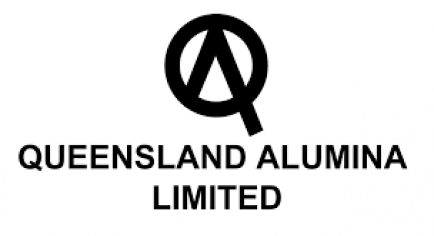
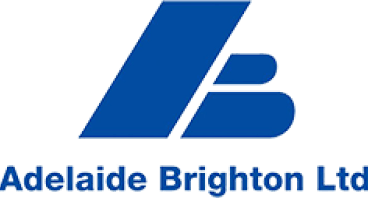


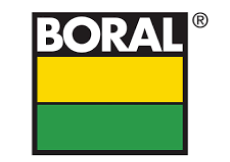



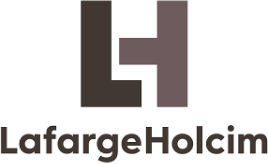
Case Studies
Failures cost money
We’ve helped dozens of industry leaders save money by thinking ahead. Come and join the success stories.
Get in Contact