Petroleum & Petrochemical
Ammonia, Methanol, Petroleum, Syngas and related plants are under pressure to reduce costs by minimising refractory maintenance scope, and yet must remain reliable while operating for extended periods between turnarounds. It is important that when refractory maintenance is carried out, it is done to engineering design standards and within budget. Due to ever increasing cost saving targets, plants now must find cost optimised solutions and adopt smart maintenance practices.
In these high pressure and temperature processes, refractory is critical to plant performance and safety as a loss of integrity can cause days, even weeks of downtime. Additional challenges such as hotspots, boiler fouling, dome failure, erosive wear can hinder plants achieving their targets.
Our Services
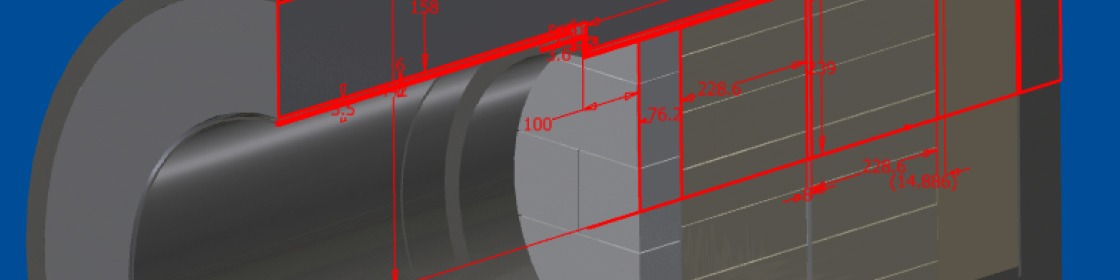
Refractory Design & Installation
Our engineered designs for reformers, transfer lines, boilers and related vessels are proven to lower the risk of refractory failure, increase lining life, simplify installation and improve plant reliability.
Additionally, we can provide quality assurance and technical support during fabrication to ensure it is built to design and that any unexpected changes are resolved efficiently and are verified from an engineering perspective and processed through your management of change system.
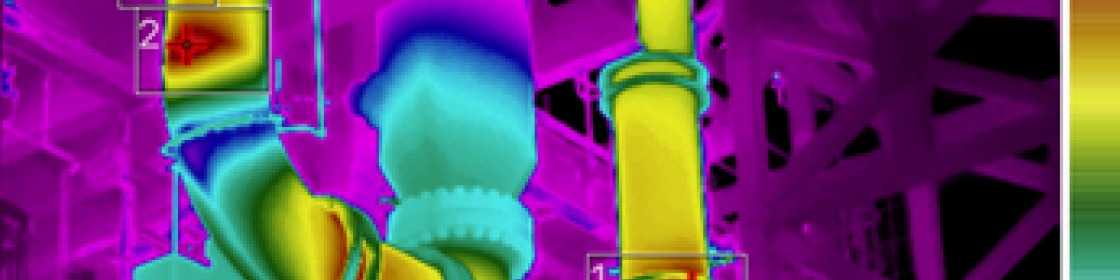
Hotspot Prevention & Analysis
It only takes a single crack to form a pathway for hot gases to create a hotspot and this effect is amplified in high pressure processes. Preventing hotspots depends on a combination of design, installation, material quality and understanding process gas interactions. We have designed and delivered many successful refractory linings that have been “hotspot free” after many years in operation. For existing hotpots, our numerical and computational analysis can identify the underlying cause so they can be eliminated during the next turnaround.
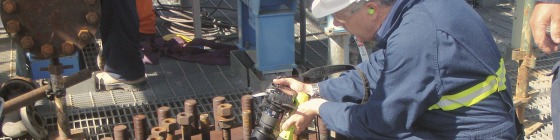
Turnaround Support
During a turnaround we can assess current refractory conditions and develop a repair scope that balances reliability and impacts to the project schedule. Additionally, we provide ‘on the spot’ professional advice by checking designs, material changes and that modifications are completed a high technical standard, within time and budget. Furthermore, we can provide an accurate scope of works for the next turnaround and advise on preventative maintenance practices.
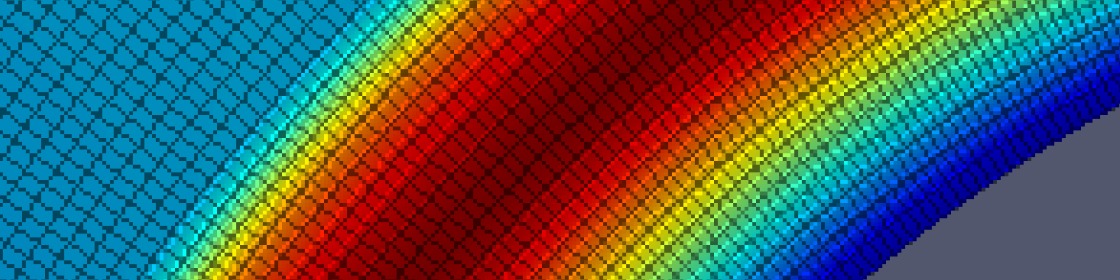
Refractory Dryouts
Typical industry dryout schedules assume ambient conditions, which does not effectively mitigate risk for pressurised processes. Additionally, these dryouts attempt to cater for all plant configurations and variations resulting in substantial inefficiencies. Our bespoke dryouts use proprietary software to calculate the most optimal, safe dryout by targeting your plant geometry, material properties, process environment and burner capacity. We have helped customers safely reduce their dryout time by over 50%.
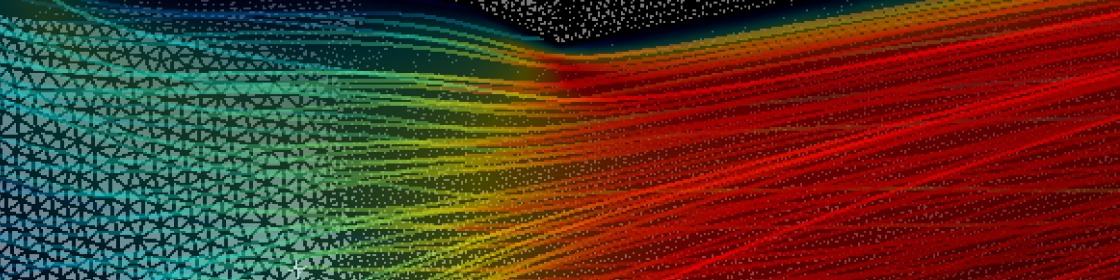
Boiler Fouling Analysis
We take a combined process and materials engineering approach to determine the root cause of process side fouling and provide cost effective solutions. We have worked with multiple companies experiencing fouling issues and successfully identified the cause and to help them eliminate the fouling.
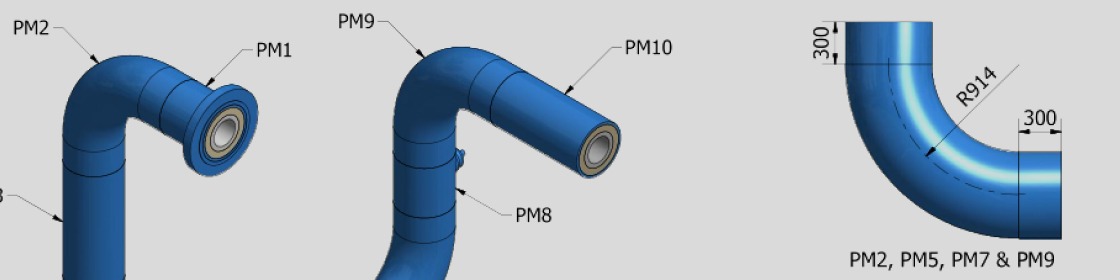
Transfer Line Refractory Design
Companies do not want to outlay a significant capital expense to replace a transfer line only for a hotspot to show up on start-up. Due to the high process velocities combined with high internal pressure, transfer lines are particularly susceptible to hotspots.
We have an optimised refractory design for transfer lines that addresses the risk of hotspots with a robust defence-in-depth approach. Our in-depth understanding of the interaction of refractory design with the thermomechanical strains specific to these components has produce great results for a range of companies.
It is critically important in preventing hotspots that refractory design meets our required standards and ensuring it is installed as per specification. We can oversee the installation to provide quality assurance, technical support and management of change.
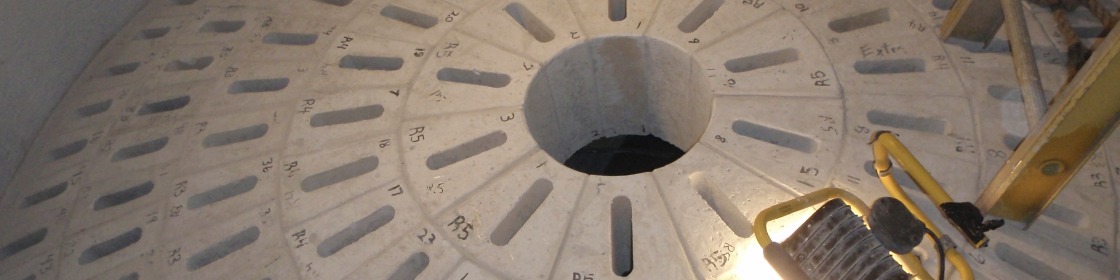
Reformer Dome Design
We can install or replace domes with our proven design which is low cost and can easily be retrofitted to almost any secondary reformer vessel or alike. This specialised dome design significantly reduces the costs compared to standard domes by simplifying construction and installation. Additionally, the design considerably reduces the risk of dome failure and has been used successfully in multiple plants.
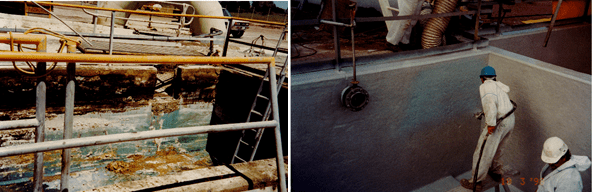
Concrete Assessment & Repairs
We specialise in the assessment of concrete structures degraded by corrosion, chemical attack, thermal stress, weathering. We undertake assessment of your structures, identify key failure mechanisms, and carry out repairs. Our experts are familiar with silos, stacks, sulphur pits, effluent tanks, plinths, columns, and other structures.
Our Clients

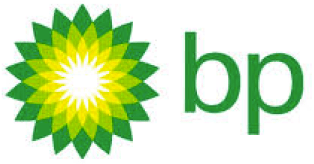




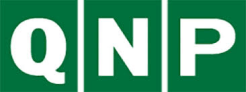


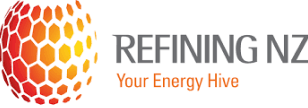


Case Studies
Save Money & Reduce Downtime
We’ve helped dozens of industry leaders save money by thinking ahead. Come and join the success stories.
Get in Contact